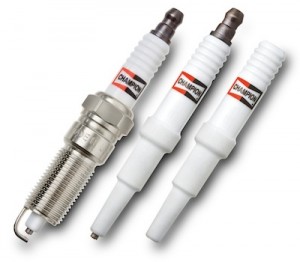
Sure Fire Plus spark plugs use a high-alumina insulator material to provide higher voltages without electrical breakdown and fit into the tighter packaging windows used in modern gasoline engines. (Credit: Federal-Mogul.)
Federal-Mogul Corp., a Southfield, Mich.-based supplier of OEM and aftermarket automotive components and systems, has introduced a new high-performance spark plug featuring a high-alumina insulator material that enables the plug to handle the increasing thermal, voltage, and other requirements of modern high-output gasoline engines.
The company’s SureFire Plus spark plugs provide higher voltages, extend plug life, and are designed to fit efficiently into the increasingly crowded engine cylinder heads, according to a news release.
Trends in modern gasoline engine technology include the need to maintain or increase performance while lowering CO2 emissions. Downsized engines with high compression ratios produce much higher peak temperatures and pressures during combustion, and use leaner air-fuel mixtures and alternative fuels that are more difficult to ignite. All these factors increase the energy requirement and thus the voltage needed across the spark plug, according to the release. Coupled with reduced real estate for the spark plug in the cylinder head—the result of smaller cylinder diameters, more valves per cylinder, and direct fuel injection technology—these changes led Federal-Mogul to develop a better insulator material that would enable high-voltage ignition and fit in a smaller package.
Rich Keller, director of product ignition engineering, says the new spark plugs can handle voltages of 42 kV or more, compared to 36 kV for the previous generation of plugs. “The ceramic insulator is the only barrier between the electrodes,” Keller says in the release. “It forces the spark to jump the gap, which initiates combustion. The unprecedented level of ceramic performance we have achieved in SureFire Plus spark plugs enables a new generation of ignition systems that provide greater energy and durability in a smaller package.”
Keller says the down-sized insulator is also a big deal. “Traditionally, spark plugs have used a 14-mm thread body,” he explains. “Today, most new engines are coming out with 12-mm thread bodies. In the future, we see this going to 10 mm in size.”
According to the release, spark plug insulators have typically been produced from a material consisting of 95 percent alumina and 5 percent glass. The insulator material in the new plugs is nearly pure alumina doped with small amounts of other oxides designed to improve high-temperature shunt resistance and minimize electrical current leakage through the ceramic.
Keller says the advanced insulator material required changes in processing methods and equipment. “In production of SureFire Plus plugs, we’ve gone from 8,500 psi compaction pressure to 30,000 psi,” he explains. “We are also heat treating the blanks to make sure we can handle them without breaking them.
The company is currently in pilot production with the new plugs; high-volume manufacturing is slated to start in May 2014. According to the release, Federal-Mogul also expects non-automotive applications for the patent-pending material, such as in the compressed natural gas market.
Linked: ACerS